Оптимизация руками изобретателей
В пятницу состоялось 27е по счету вручение Бардинской премии
Церемония этого года для лауреатов и для всех сотрудников ЧерМК ОАО «Северсталь» стала особенной: во многом именно благодаря усилиям собравшихся в зале торжеств Дворца металлургов предприятие смогло благополучно преодолеть сложную ситуацию экономического кризиса. Оптимизация, новые рынки сбыта, новые уникальные и ресурсоемкие технологии — за достижения именно в этих сферах вчера работникам ЧерМК вручали заслуженные награды. Лауретами премии становились не только инженеры. «Мы налаживали сбыт новой, современной продукции комбината в Иране», — рассказывает Владимир Рахуба, менеджер дирекции по сбыту (на фото).
Символично, что церемония состоялась в день рождения академика Бардина, чьим именем названа премия. В общей сложности дипломы и нагрудные знаки получили 69 лауреатов конкурса — среди них оказались не только череповчане: приехали и сотрудники колпинской площадки ОАО «Северсталь», расположенной в Ленинградской области.
Премию всегда вручали за инновации — но никогда они не были так важны для производства, как в 2009 году, подчеркнул технический директор и главный инженер ЧерМК Андрей Луценко:
— Сегодня шанс на успех, на долговременное пребывание на рынке есть только у тех компаний, которые умеют найти нестандартные, но эффективные решения самым сложным задачам.
Одной из особо отмеченных работ, победивших в конкурсе на соискание премии, оказалась коллективная разработка коксохимиков.
— Наш проект называется «Внедрение метода сквозной горячей перекладки для продления срока эксплуатации коксовых батарей № 9 — 10», — рассказывает Татьяна Гагарина, специалист коксохимического производства. — Дело в том, что срок действия таких батарей, содержащих 65 коксовых печей, — 20 лет. Далее происходит следующее: кладка стен коксовых печей разрушается, требуется ремонт — а так как длина печи 16 метров, высота 5,5, а температура внутри — от 1000 до 15000 С, то ремонт представляется практически невозможным. Таким образом, вместо экономичного ремонта требуется замена оборудования. Наша идея сквозного ремонта оказалась решением этой проблемы.
Сама идея принадлежит начальнику КХП Александру Габову, и в успешный результат изначально — в 2005 году, когда проект начал разрабатываться, — мало кто верил. Основная особенность в том, что ремонт проводится в действующем цехе без приостановки всей батареи коксовых печей — температура соседних с ремонтируемой печей только снижается с 1000 до 8000 С. Их кладка оклеивается современным теплоизоляционным материалом, что позволяет поддерживать на месте ремонта температуру в 50 — 600 С. Это хоть и тяжелые, но уже приемлемые для работы условия.
— Над ремонтом одной печи трудятся более ста огнеупорщиков, и те 800 миллионов экономии, которые получил комбинат благодаря нашему проекту, большей частью являются заслугой именно этих людей, — считает Татьяна Сергеевна.
Не только инженеры получали премии — наградили и менеджеров, сотрудников отдела сбыта:
— В первую очередь то, что мы сделали, позволило нам получить выгодные заказы: мы налаживали сбыт новой, современной продукции комбината в Иране, — рассказывает Владимир Рахуба, менеджер дирекции по сбыту. Проект «Освоение и внедрения технологии производства проката для поставок автомобильным компаниям Иранской республики» — коллективный, работа над поставками металла в Иран велась с 2005 года.
— Конечно, эта страна не сможет стать ключевым рынком сбыта для нас — конкуренция и затраты на доставку дают о себе знать, но, по крайней мере, мы лидируем среди других российских производств на рынке автомобилестроения Ирана. Кроме того, это сотрудничество дает нам не только прибыль, но и опыт производства автомобильных материалов, непривычных для России. И в итоге, когда все эти технологии появятся в нашей стране, мы будем готовы поддерживать своей продукцией и отечественное автомобилестроение, — объясняет Владимир Валерьевич.
Елена Срапян
№213(22623)
17.10.2009
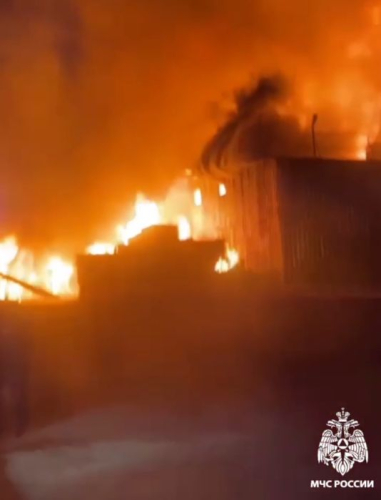
1500 квадратных метров охватило пламя на лесопильном предприятии в посёлке Новатор
С огнём всю ночь боролись более пяти десятков человек →
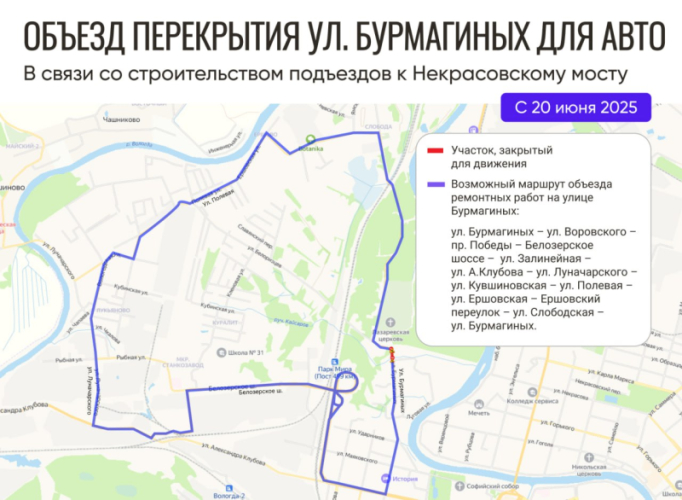
Проехать в парк Мира на автомобиле всё лето можно только со стороны Ботанического сада
Участок улицы Бурмагиных рядом с Лазаревской церковью перекрыт для движения транспорта на срок до конца ноября →